TECHNOLOGICAL
INNOVATION
技术创新
Advanced production machinery and equipment solve the traditional problems and pain points in the industry, making product quality and stability stand out among peers
TECHNOLOGICAL
INNOVATION
技术创新
Advanced production machinery and equipment solve the traditional problems and pain points in the industry, making product quality and stability stand out among peers
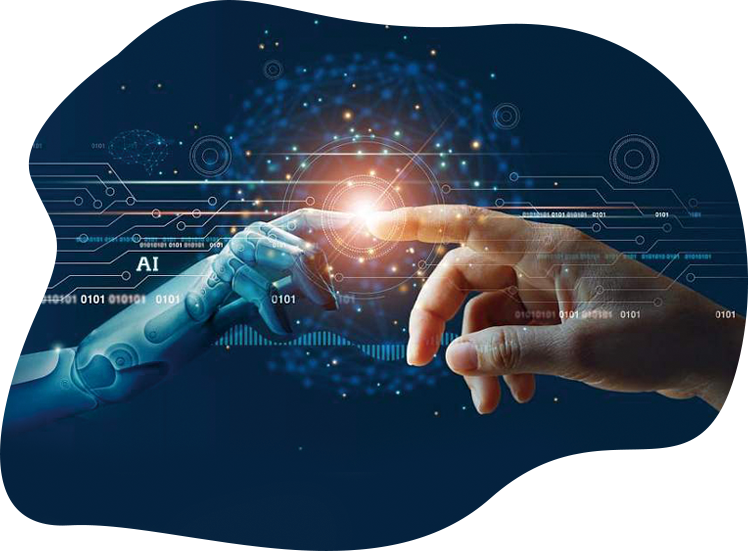


01.
High-precision Warp Monitoring Instrument
Takefast uses a high-precision warp monitoring instrument to solve four major abnormalities brought by traditional production: uneven tension, inconsistent thickness, color depth variations of the same belt, and large deviation in loop position, ensuring high product quality.
Traditional Weighting Method
Operators need to constantly add and subtract weights, which is easy to overlook, causing webbing elasticity to vary greatly.
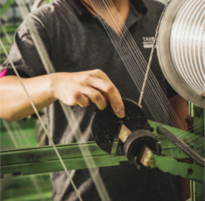
VS
Warp Monitoring Adjustment Method
Electronic data monitoring throughout the process, significant tension control effect, reducing losses, and stabilizing tension.

02.
Mobile Stretch Tester
The mobile stretch tester is fast, lightweight, flexible, and can be moved freely without needing a power source, air compressor, or cutting band pneumatic fixture. It can be tested directly with a hook, testing force 0~10KGF60S, capable of continuous testing twice, providing accurate and professional test data. In addition to providing tensile data and exporting tensile graphs, it can also automatically measure the temperature and humidity of the workshop.
Mobile Stretch Tester
Can test tensile data at any time during the production process, precise, efficient, convenient, and fast.
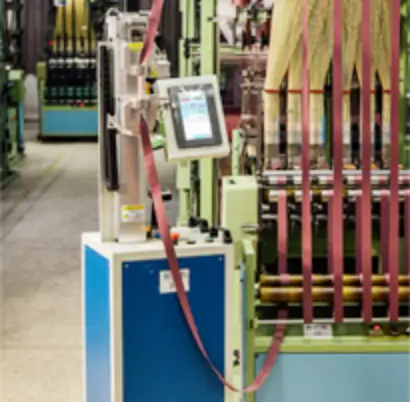
VS
Warp Monitoring Adjustment Method
Cannot be moved arbitrarily, cannot provide tensile test data at any time.
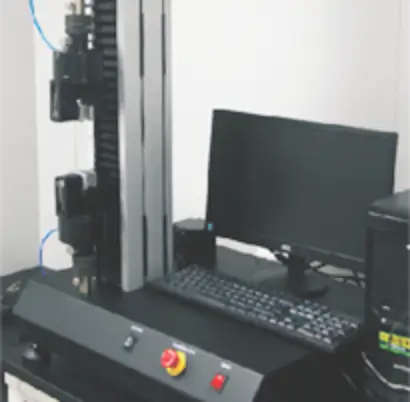
03.
Fully Automatic Dyeing Machine Additive Monitoring System
The post-processing equipment in the webbing dyeing industry is relatively primitive, making it difficult to implement production processes, leading to a high rework rate and severely hindering production. The fully automatic additive monitoring system of the dyeing machine perfectly solves the post-processing process implementation problems.
Traditional Manual Additive
According to fabric product requirements, employees manually add pre-mixed additives, which is easy to miss, causing waste and unstable quality.
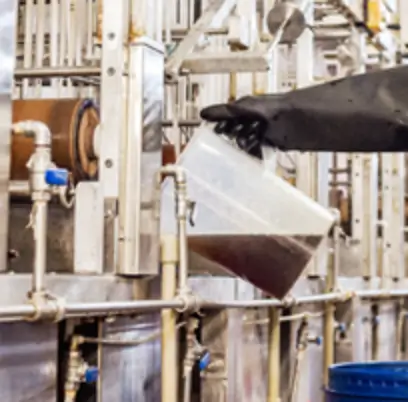
VS
Fully Automatic Additive Detection System
Use intelligent detection instruments to detect the active ingredients in the production solution in real-time, accurately supplementing, making the production process perfect and running throughout the entire production process.
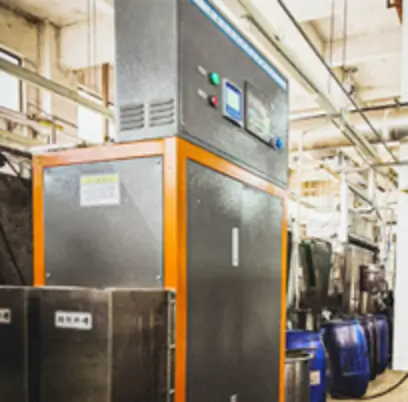
04.
Automatic Powder Dispensing System
Traditional manual powder weighing is inefficient, time-consuming, and inaccurate. The powder dispensing system connects to the ERP system, automatically linking system documents, and accurately measuring quantities, improving efficiency and accuracy.
Traditional Manual Weighing
Manual document verification and weighing are time-consuming and inaccurate.
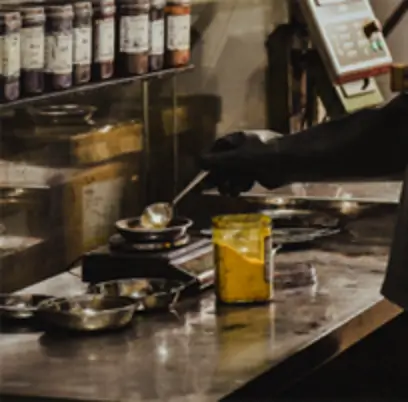
VS
Automatic Powder Dispensing System
Cannot be moved arbitrarily, cannot provide tensile test data at any time.
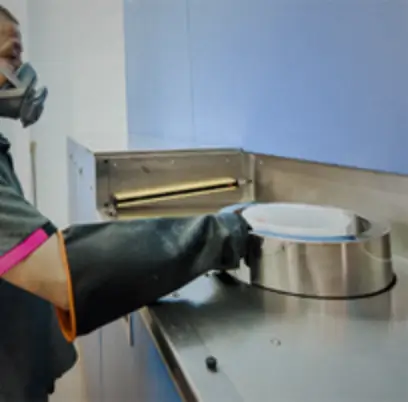
Quality Control
Every product of Takefast Textile is tested and inspected according to the technical specifications and international standards required by customers. Continuous independent inspection 24 hours a day ensures product quality, building customer confidence in Takefast Textile.
Raw material control
Raw yarns are supplied by well-known suppliers in the industry: Nustar, Jinjiang, Dehua, Meida, etc., controlling product quality from the source. As market business continues to expand, the types of yarns are also increasing, including mint yarn, environmentally friendly yarn, moisture-wicking yarn, antibacterial yarn, etc.
All incoming yarns are inspected and tested as required to ensure that the materials used in production meet the requirements, ensuring product quality.
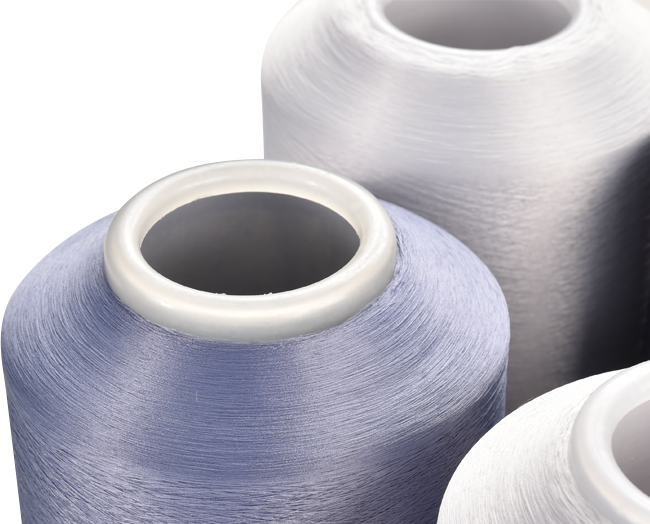
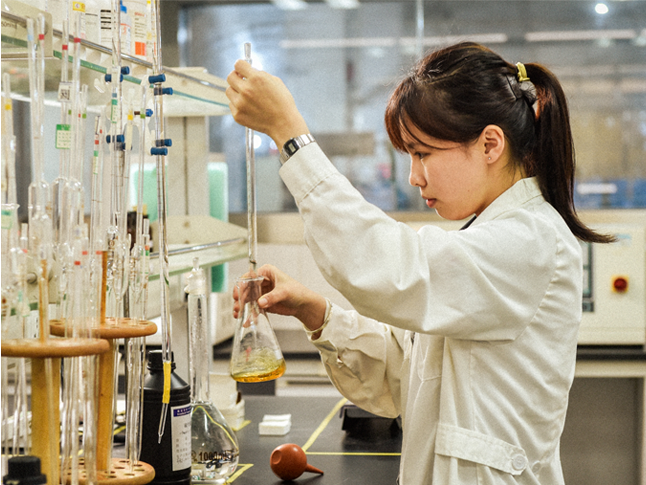
Laboratory
Well-equipped laboratories with clearly defined process operation procedures ensure reasonable and effective control of quality during the webbing process, reducing the occurrence of defective products. Safeguarding new product development and mass production.
In addition to various routine tests, laboratory testing projects include seawater colorfastness, chlorine water colorfastness, chlorine bleaching colorfastness, lightfastness, color migration, high-temperature aging.